By Paul Cook
Shutdowns involve significant costs and can impact supply chains and customer relationships. In 2005, Advanced Technology Services, a provider of equipment maintenance and spare parts, and Nielsen Research surveyed 101 automotive executives who said stopped production costs on average $22,000 per minute. That’s why companies look to make a shutdown as efficient and short as possible.

With persistent material and labor shortages, many companies are thinking of cancelling their year-end planned shutdown in 2021 and at least the first half of 2022. That choice carries a risk. In 2019, research from ServiceMax and GE Digital found “82 percent of manufacturing firms have experienced unplanned downtime in the last three years, with an average cost of $260,000 per hour.”
Many facility executives cancelled or modified their 2020 planned shutdowns because of the pandemic, resulting in more maintenance deferrals. Meanwhile, operational wear and tear continues — accelerated in some cases — on facilities and equipment.
Industrial cleaning, painting, and flooring services can be highly disruptive to normal operations, so these projects are mainstays of planned shutdowns. Following are five rules for shutdowns (and slowdowns) that will enable facility owners and operators to get more done in less time, prevent unplanned shutdowns, and save money.
1) Assess priorities based on need and value. Assessing maintenance priorities is a never-ending task for facility managers who juggle production schedules, operational goals, and budgets. Organizing for a shutdown is a matter of triage and prioritizing what’s necessary versus discretionary. Prioritizing helps facility owners and operators assess needs and make decisions that keep a project within a deadline and budget.
- Consider your KPIs (Key Performance Indicators). Typical maintenance KPIs include the facility’s safety record, supply chain requirements, material and labor costs, and production schedules.
- Evaluate the seriousness and urgency of your needs. Sort maintenance into categories like low, medium, and high; cracks, leaks, rust, and sputtering machinery, for example, are high. To help rank your needs, consider using a computerized maintenance management system (CMMS) to assign priorities to projects and people.
- Think about workplace safety hazards or business concerns like food safety and hygiene. Passing facility inspection requirements, complying with necessary regulations, and exposure to liabilities are a priority.
- Manage your risk and inspection readiness. Consider safety violations, inspection failures, legal exposure, unplanned disruptions, and financial risk if you defer a project.
2) Marry scope of work and available time. Managers must ensure they’ve accurately aligned the time and circumstances for each task. Often, they have more projects than downtime, and even when projects match available time, interruptions happen.
- Tap data from prior maintenance projects. Review spreadsheets, project management plans, and vendor documents. Enlist the help of your facility management software systems to extract data. If you find yourself with poorly created or disorganized records, consider this an opportunity to clean up record-keeping and documentation.
- Consult contractors. Call on contractors you’ve either worked with successfully in the past or with the competence to match your requirements. Ask for references, review ISN profiles, and check certifications, and capability statements to make sure they merit your trust.
- Identify time-consuming steps and timeline constraints. For painting and coating projects, that includes tasks like proper surface preparation and adequate drying and curing time. Don’t cut corners to save time; it compromises quality and safety and leads to unplanned disruptions.
- Consider a project’s complexity. For large facilities or complex projects, boosting the size of the work crews and using time-saving processes (e.g., moving equipment before crews arrive, so you’re not waiting for maintenance personnel to tackle the work) and materials can reduce maintenance timelines without compromising quality.
You may know how much time your facility maintenance project will need. But as a reference, below are examples of projects we’ve accomplished, along with the time they took.

3) Plan and communicate early and often. The more you can do in advance, the better, especially if your maintenance plans will be more of a small stop or slow-down and not a full planned shutdown. Preparation should involve both external contractors plus your internal stakeholders and participants, including work teams that will be on-site when maintenance work is performed.
- Work in advance with external providers. Walk-through inspections by contractors with professional certifications and credentials detect problems and lead to accurate estimates of the scope and length of work.
- Stay in touch with internal stakeholders. Gain support from everyone who could be affected by maintenance work; contractors often arrive and find they’re dealing with the client’s shift teams who are unaware maintenance work will be done as they’re trying to do their jobs.
- Create a good maintenance plan. Develop a work package, even for brief shutdowns that includes: job description; number of workers; estimated labor hours; and scheduling details like safety precautions, security rules, and shift hours.
It’s not enough to simply send out a message. Make sure your employees acknowledge receiving it.
For example, we had a small flooring-joint reconstruction project with a 12-hour timeline including curing. During curing, there can be no forklifts or heavy traffic on the surface. The facility scheduled the work to begin at 2 p.m., after peak operations and allowing for much of the epoxy cure time to take place overnight. Our crew arrived and saw the flooring area had palletized products everywhere. The facility’s employees hadn’t been informed, and they didn’t want their work interrupted. Our crew said they could repair the joints by working in sections and covering the palletized product to protect the contents, which pleased the employees. Ultimately, we finished the job correctly and safely within 12 hours.
Lesson: A stakeholder may learn of a maintenance plan and say nothing, agree, or fail to disagree. Stakeholders often forget or have a change of heart. There must be a final check-in with the stakeholder and team, before starting maintenance work, and a contractor who can improvise.
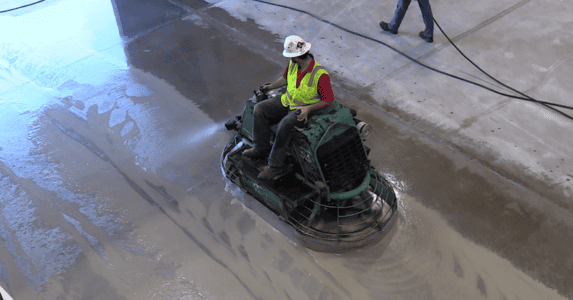
4) Leverage data to minimize maintenance time. Like other areas of a company’s operations, facility maintenance should be driven by data too.
- Compare actual vs. estimated labor hours and actual vs. budgeted costs. Documenting the outcome of previous projects and reviewing these prior to new ones gives managers not only a benchmark but also helps vet contractors’ estimates for new jobs.
- Improve current and future planning and budgets. If you find yourself with poorly created or disorganized records, commit to enhancing your record-keeping and documentation efforts by moving to a CMMS, which integrates with other enterprise data-collection and planning tools your company may use.
- Help new managers and teams tapped for future shutdowns. Succession planning is always a hot topic for C-suite executives, but every facility executive should have a succession plan, too, and part of those plans require introducing new managers and teams to all the elements of the current manager’s job, including planned maintenance during shutdowns.
5) Select the right people, processes, and materials. Working with the right contractors who will help you identify the best processes and choose the right materials and supplies is crucial to getting work done fast, like during second or third shifts or weekend hours.
- Question the lowest bid. Before opting for the least-expensive option, compare the low-bid contractor’s scope of work with other bids to see what, if anything, might be left out (e.g., an extra topcoat, extra drying time) or whether the quality or grade of material is less likely to hold up under heavy traffic.
- Look for contractors with cred. Your contractor should have experience meeting deadlines, well-trained crews especially for big projects, OSHA safety credentials, and a safety record as measured by TRIR (Total Recordable Incident Rate) and the EMR (Experience Modifier Rate).
- Consider diversity in suppliers. If your organization has a supplier diversity program, then include veteran-, minority- and woman-owned businesses. All industries and trades have professional programs and associations that validate a contractor’s capabilities, like the National Center for Construction Education and Research, or NCCER. For corrosion and coatings expertise, look to NACE, now AMPP – Association for Materials Protection and Performance. And groups like the Women’s Business Enterprise National Council, or WBENC, certify that business claiming to be woman-owned truly are. These credentials and certifications ensure the vendor has the credentials and expertise you need.
- Plan for quality control and assurance. Add any work that doesn’t meet your contractor’s assurances to a punch list for corrections.
Remember Why Maintenance Matters
Deferred maintenance is sometimes necessary, but you can push luck only so far. Instead of simply cataloguing your maintenance issues, consider turning those assessments into a financial-risk model by analyzing what risk looks like. Look at something tactical like the condition of your facility’s roof and turn that into an analysis that your financial team can use to direct spending. In other words, determine the condition of your assets, where the gaps are, and add up the financial cost of inaction (e.g., if we don’t repair this roof and it leaks, then what is the cost of shutting down and repairing water-damaged equipment, spoiled product or lost shipments?).
Remember these points as you prepare arguments for an executive team that questions the need for a planned shutdown, or more likely, feels intense pressure to maintain production and operations, often around the clock.
Cook is vice president of Painters USA Inc., where he has worked since 1976. He is NACE Coatings Inspector Level 1 – Certified (Cert. No. 48833). Painters USA is a nationwide, woman-owned, WBENC-certified provider of commercial and industrial flooring, cleaning and painting services.